Epoxy Marine Edges
- Lab furniture countertop epoxy marine edges are specialized components engineered to shield laboratory furniture from the detrimental effects of corrosive liquids.
- Composed of high – purity epoxy resin, these protective elements are meticulously integrated into the joints, edges, and seams of lab furniture.
- Their core function is to erect an impermeable barricade, effectively halting water ingress stemming from spills, condensation, or the generally humid lab environment.
- Specialized additives are incorporated into the resin to augment chemical resistance and biocompatibility.
- This enables the these edges to endure the harsh conditions prevalent in laboratories while safeguarding stored chemicals, reagents, samples, and sensitive equipment.
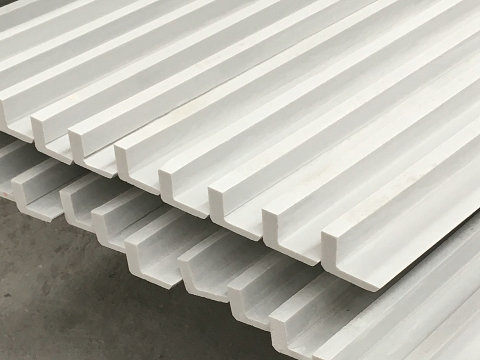
Water and Chemical Resistance
- Epoxy marine edges showcase exceptional water resistance. They form a dense and continuous seal that efficiently blocks moisture.
- In laboratories where accidental spills of water based solutions are a common occurrence, these epoxy hydro resistant trims act as a bulwark, preventing water from infiltrating the furniture’s structure.
- This, in turn, averts issues such as swelling, warping, or mold growth. Their chemical resistance is equally impressive.
- Laboratories are rife with a wide array of aggressive chemicals, and it can resist the corrosive impact of acids, alkalis, and organic solvents.
- This protective function significantly extends the lifespan of lab furniture, maintaining its structural integrity and functionality over an extended period.
Compatibility and Durability
- Epoxy marine edges exhibit high compatibility with diverse materials used in lab furniture construction, including stainless steel, wood, and synthetic polymers.
- They adhere tenaciously to these surfaces, creating a seamless bond that neither compromises the furniture’s aesthetic appeal nor its usability. Their durability is remarkable.
- Capable of withstanding mechanical stress, such as impacts and vibrations that frequently occur in bustling laboratory settings, these profiles ensure long – term performance, minimizing the need for frequent replacements.
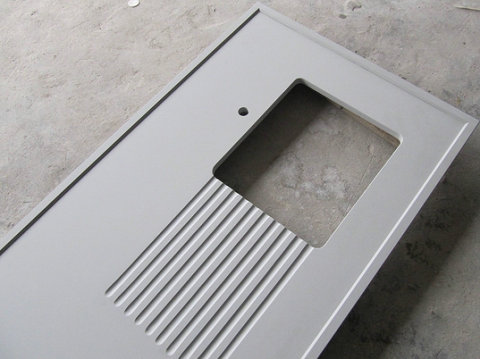
Material Preparation
- The production of these essential lab components, including epoxy marine edges, begins with a meticulous material selection process. High – quality epoxy resin, renowned for its outstanding adhesive and curing properties, forms the basis.
- Specialized additives, tailored to meet the unique demands of laboratory use, are accurately measured.
- Additionally, for epoxy resin edges, specific materials and techniques are employed to ensure durability and resistance in potentially humid and corrosive laboratory environments. This painstaking material preparation is fundamental to producing reliable and effective water blocking solutions, including those with epoxy marine edges.
Manufacturing and Assembly
- The epoxy resin and additives are thoroughly blended to create a homogeneous mixture, which is then used to manufacture epoxy marine edges. These barriers are designed to be highly effective in water – blocking applications within the laboratory environment.
- The combined material is shaped into protective strips using precision molds, which define their dimensions and surface finish. After molding, the products, including the epoxy aquatic barriers, undergo a curing process.
- This can occur at room temperature or be expedited with heat assistance to harden the epoxy resin. Once cured, they are ready for installation onto lab furniture. They are carefully positioned and firmly bonded to critical areas where water resistance is crucial, such as the edges and joints of lab countertops and cabinets.
Workbenches and Fume Hoods
- Epoxy marine edges are applied to the edges and joints of workbenches, creating a protective shield.
- Workbenches in labs are frequently exposed to spills and splashes during experiments.
- Fume hoods, which handle hazardous chemicals and may generate condensation, also benefit significantly from these trims.
- By preventing water accumulation and chemical leakage, they enhance the safety and functionality of these essential lab furniture components, protecting both the furniture and the laboratory personnel.
Technological Advancements
- The future of lab furniture protective elements lies in technological innovation.
- Researchers are actively exploring the development of self – healing epoxy formulations. These novel materials would be capable of repairing minor cracks or damage caused by chemical exposure or mechanical stress, further elongating the lifespan of products like epoxy marine edges.
- Additionally, the integration of smart sensors into these components is on the horizon. These sensors could detect early signs of water leakage or material degradation, enabling proactive maintenance and preventing potential damage to lab furniture and valuable research materials.
Customization and Sustainability
- Epoxy marine edges, with their unique properties, are expected to play a significant role in this customization trend, providing enhanced durability and water resistance. Moreover, sustainability will be a key focal point.
- The use of bio – based epoxy resins in production will mitigate the environmental impact, aligning with the growing emphasis on green laboratory practices.
- As laboratory requirements become increasingly diverse, there will be a burgeoning demand for customized solutions. Manufacturers will concentrate on developing products tailored to specific types of lab furniture and research needs.